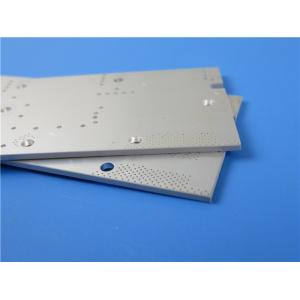
Add to Cart
High Frequency PCB Built on Taconic RF-60A 60mil 1.5mm Core With Immersion Silver For
Power Amplifiers
(Printed Circuit Boards are custom-made products, the picture and parameters shown are just for
reference)
RF-60A is a cutting-edge organic-ceramic laminate within Taconic's ORganic CERamic (ORCER)
product line, engineered with a foundation of woven glass reinforcement. This innovative material
represents the culmination of Taconic's proficiency in ceramic fill technology and coated PTFE
fiberglass. RF-60A boasts remarkable interlaminar bond strength and resistance to solder,
showcasing its robust construction.
The proprietary formulation of RF-60A contributes to its outstanding performance attributes,
including low moisture absorption and consistent electrical properties across the material.
This unique blend of characteristics makes RF-60A an ideal choice for applications where
reliability, durability, and precise electrical performance are essential.
RF-60A's woven glass reinforcement plays a pivotal role in ensuring exceptional dimensional
stability and bolstering flexural strength, making it a robust choice for demanding applications.
This reinforcement also contributes to low Z-axis expansion, fostering plated-through-hole
reliability even in extreme thermal environments.
Featuring a dielectric constant of approximately 6.15, RF-60A stands out as an ideal high DK
(dielectric constant) material for applications necessitating compact circuit dimensions and
reduced weight. Its low electrical loss factor further enhances its suitability for RF circuits,
ensuring minimal signal degradation and optimal performance in high-frequency applications.
RF-60A excels in providing a balance of mechanical strength, thermal reliability, and electrical
performance, making it a versatile solution for a wide range of advanced electronic designs.
RF-60A laminates adhere fully to RoHS and WEEE directives, ensuring environmental compliance,
and are designed to meet the temperature requirements associated with lead-free soldering processes.
Their compatibility with these soldering techniques makes them suitable for modern manufacturing standards.
These laminates can undergo shearing, drilling, milling, and plating using standard methods applicable
to PTFE-woven fiberglass materials. This feature streamlines the production process, facilitating mass
production and enabling efficient manufacturing operations. The versatility and ease of processing of
RF-60A laminates make them a practical choice for a variety of industrial applications requiring precision
manufacturing and compliance with environmental regulations.
Our PCB Capabilities (RF-60A)
PCB Material: | Organic-ceramic Woven Fiberglass Reinforced Laminates |
Designation: | RF-60A |
Dielectric constant: | 6.15 ±0.25 |
Dissipation Factor | DF 0.0038@10 GHz |
Thermal Conductivity | 0.4 W/MK |
Layer count: | Double Layer, Multilayer, Hybrid PCB |
Copper weight: | 0.5oz (17 µm), 1oz (35µm), 2oz (70µm) |
PCB thickness: | 10mil (0.254mm), 25mil (0.635mm), 31mil (0.787mm), 50mil (1.27mm), 60mil (1.524mm), 125mil (3.175mm) |
PCB size: | ≤400mm X 500mm |
Solder mask: | Green, Black, Blue, Yellow, Red etc. |
Surface finish: | Bare copper, HASL, ENIG, OSP, Immersion tin etc.. |
Benefits (in general):
Low Moisture Absorption
Stable DK over Frequency
Dimensionally Stable
Low Z-axis Expansion
High Flexural Strength
Exceptional Interlaminar Bonds
Typical Applications:
Power Amplifiers
Filters & Couplers
Passive Components
Antennas
Data Sheet of Taconic RF-60A
Property | Test Method | Unit | Value | Unit | Value |
Dk @ 10 GHz | IPC-650 2.5.5.6 | 6.15 | 6.15 | ||
Df @ 10 GHz | IPC-650 2.5.5.5.1 | 0.0038 | 0.0038 | ||
Moisture Absorption | IPC-650 2.6.2.1 | % | 0.02 | % | 0.02 |
Dielectric Breakdown | IPC-650 2.5.6 | kV | 53 | kV | 53 |
Dielectric Strength | ASTM D 149 | V/mil | 880 | kV/mm | 35 |
Volume Resistivity | IPC-650 2.5.17.1 (After Humidity) | Mohm/cm | 9.0 x 108 | Mohm/cm | 9.0 x 108 |
Surface Resistivity | IPC-650 2.5.17.1 (After Humidity) | Mohm | 2.28 x 108 | Mohm | 2.28 x 108 |
Arc Resistance | IPC-650 2.5.1 | Seconds | 193 | Seconds | 193 |
Flexural Strength (MD) | ASTM D 790 | psi | 18,300 | N/mm2 | 126.2 |
Flexural Strength (CD) | ASTM D 790 | psi | 14,600 | N/mm2 | 100.7 |
Tensile Strength (MD) | ASTM D 3039 | psi | 19,500 | N/mm2 | 134.4 |
Tensile Strength (CD) | ASTM D 3039 | psi | 16,300 | N/mm2 | 112.4 |
Young’s Modulus | ASTM D 3039 | kpsi | 1,590 | N/mm2 | 11,000 |
Poisson’s Ratio | ASTM D 3039 | 0.068 | N/mm2 | 0.068 | |
Compressive Modulus | ASTM D 695 (23°C) | kpsi | 338 | 2,330 | |
Peel Strength (1 oz. ED) | IPC-650 2.4.8 Sec. 5.2.2 (Thermal Stress) | lbs/in | 8 | N/mm | 1.4 |
Dimensional Stability (MD) | IPC-650 2.4.39 Sec. 5.4 (After Bake) | mils/in | 0.68 | mm/M | 0.68 |
Dimensional Stability (CD) | IPC-650 2.4.39 Sec. 5.4 (After Bake) | mils/in | 1.05 | mm/M | 1.05 |
Density (Specific Gravity) | ASTM D 792 | g/cm3 | 2.79 | g/cm3 | 2.79 |
Thermal Conductivity | ASTM F 433 | W/M*K | 0.4 | W/M*K | 0.4 |
CTE (X axis) | ASTM D 3386 (-30°C - 125°C) | ppm/°C | 9 | ppm/°C | 9 |
CTE (Y axis) | ASTM D 3386 (-30°C - 125°C) | ppm/°C | 8 | ppm/°C | 8 |
CTE (Z axis) | ASTM D 3386 (-30°C - 125°C) | ppm/°C | 69 | ppm/°C | 69 |
Outgassing (% TML) | ASTM E 595* | % | 0.02 | % | 0.02 |
Outgassing (% CVCM) | ASTM E 595* | % | 0.00 | % | 0.00 |
Outgassing (% WVR) | ASTM E 595* | % | 0.01 | % | 0.01 |
Flammability Rating | UL 94 | V-0 | V-0 |